Plastic pollution is a global crisis; however, plastic recycling washing machines lines offer a successful answer. These systems clean, shred, and recycle scrap plastic available to be used again. It promotes the circular economy and protects the earth. Understanding how these equipment work can assist recycling and eco-conscious manufacturers manage plastic waste.
Find out how a plastic recycling washing machine that recycles plastic changes waste into materials that can be used again. learn the benefits of these systems, how they may work, and how to choose the right one for what you need.
In this guide, we’ll cover:- A plastic recycling washing line is a system that purifies, shreds and turns recycled plastics into materials that are usable and utilized again. This is the fact in multiple stages.
- To effectively remove pollution from plastic waste, it comes in vital components such as shredders, washers, float-sink tanks, and dryers.
- This technique raises the value of items, drops the sum of energy used, and helps recycling go on in a circular economy.
- Consider factors like plastic kind, processing capacity, contamination levels, and system efficiency when selecting a washing line.
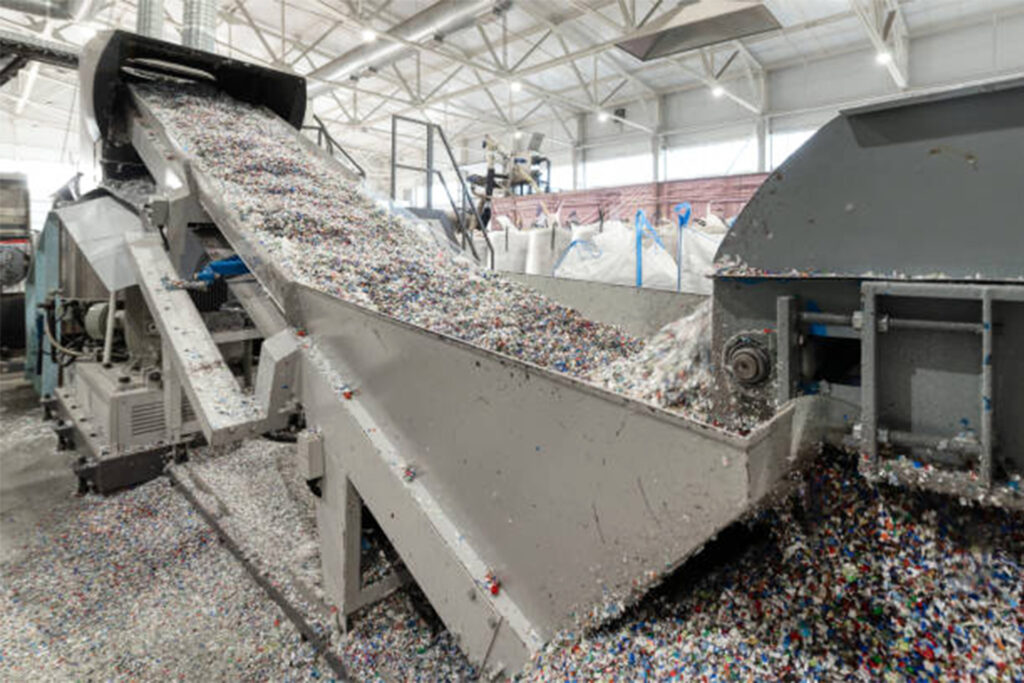
What Is a Plastic Recycle Washing Line?
An industrial system named a plastic recycling washing line is designed to clean, shred, and convert waste plastics into raw materials that can be reused again. Similar to an exclusive plastic recycling washing machine, a full washing line contains multiple machines that partner to:
- Remove pollutants, labels, and dirt.
- Shred plastic into tiny pieces.
- Dry and wash the material for reuse directly or by pelletizing it.
For reuse facilities, plastic manufacturers, and waste management organizations seeking to turn plastic waste into valuable assets, such techniques are essential.
Why Washing Lines Matter in Recycling
Unlike standalone washing units, complete washing lines offer:
- Comprehensive contaminant removal
- Higher processing capacities
- Better quality output
- More efficient water and energy use、
How Plastic Recycling Washing Lines Work?
There is a thoughtful system for the plastic washing technique that enables maximum cleaning efficiency while minimizing the use of energy or water.
The first step is collection and sorting, which stands out the different types of plastic and disposes of non-plastic pollution like metals.
The plastic undergoes size reduction in powerful shredders or crushers in it was previously sorted. Massive items can be ground up into uniform flakes via these machines, dramatically expanding the surface area for improved washing.
After that, the particles were submitted to a multi-step washing procedure. In order to further filter the plastic stream, modern systems often incorporate float-sink separation tanks to make use of density differences.
Previous to the material entering drying systems that prepare it for the next recycling cycle, the final steps focus on removing water, with high-speed centrifuges collecting most of the moisture.

Key Components of the Plastic Recycling Washing Line
A complete plastic recycling washing machine system includes:
Component | Function |
Conveyor Belt System | Moves plastic trash from one machine to another. |
Shredder/Crusher | Transforms substantial plastic objects into particles. |
Friction Washer | Gets rid of dirt with hot water and movement. |
Float-Sink Tank | Using density to separate plastics (filters out impurities). |
Dewatering Machine | Reduces drying time by spinning water. |
Flake Drying System | Ensures moisture-free flakes for storage. |
Benefits of Professional Washing Systems
Investing in a professional plastic washing line has many advantages for recycling businesses and organizations producing plastic. The following are a few of the multiple advantages of acquiring a plastic recycling washing line:
Improving the value of material
he major benefit is the significant raise in material quality, which causes higher prices in recycling markets and more efficiency in subsequent manufacturing processes for properly cleaned plastic flakes.
Saving energy
These systems offer substantial energy savings in terms of operations.
Automatic lines process high volumes with less labor, and regular maintenance prevents downstream quality challenges. The environmental benefits are the same as compelling, with each tonne of plastic that was properly recycled in the right way saving lots of energy compared to the creation of virgin material.
Adaptability
Modern washing systems are also quite versatile; several of them can quickly switch to multiple types of plastic. As a result of this flexibility, operators have the ability to react to increasing material streams and market demands, and this impacts their recycling operations clearly for the future.
How to Choose the Right Plastic Recycling Washing Line?
When choosing an appropriate washing process for plastic, it is necessary to provide major attention to a variety of crucial rules.
Discover your needs by asking about these issues before selecting a plastic recycling washing line:
Understanding your needs
- What type of particles consisting of plastic will you process? (such as mixed plastics, PP films, PET bottles, and HDPE containers)
- What is the expected capacity for input? (such as 500 kg/h, 1 ton/h, or 5 tons/h)
- To what level is the feedstock contaminated? Like extra oil, dirt, labels, and adhesives)
- What sort of output quality is needed? (e.g., spotless flakes, pellets for high-end products)
- Is an entirely automated or semi-automated system required?
- What is your budget and how much space do you provide?
You can evaluate the required washing line equipment once these standards are known.
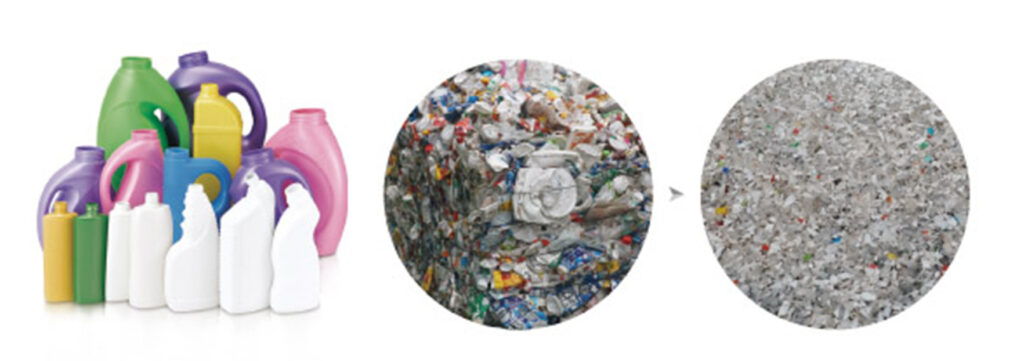
Selecting the Best Washing Line for What You Need
Below are the critical points to consider for each machine:
1. Plastic Shredder
Listed are the key elements to consider for each machine:
For ease of next steps, the plastic shredder cuts the size of large pieces of plastic waste.
Key Factors to Consider:
- Material Compatibility: Ensure that it is suitable for the type of plastic you apply (thin, rigid, flexible).
- Blade Design & Durability: Blades composed of hardened steel ask for fewer repairs and last longer.
- Output Size Control: Modifiable screen dimensions guarantee equal flake size.
- Throughput Capacity: Calculate the capacity you will process per hour or the total output you will need.
- Preventing dust and noise: It is essential to maintain the safety of workers and comply with environmental rules.
2. Plastic Granulator Machine
A granulator machine gets broken plastic into tiny, even parts called granules.
Key considerations to consider:
- Think about rotor speed and cutting efficiency, which are an influence on processing speed and particle size.
- The ultimate granule size (e.g., 6mm, 10mm) is fixed to the dimension of the screen mesh size.
- The cooling system stops material deterioration and overheating.
- It's easy to clean and change its blades, so it's relatively effortless to maintain.
3. Plastic Extruder
Pelletizing requires melting and homogenizing plastic.
Importance of Key Factors:
- The screw design, which can be either single or twin-screw, is better for plastics that are mixed or contaminated.
- Temperature control and heating zones enable proper melting without degradation.
- The filtration system (also known as a melt filter or screen changer) removes waste products.
- For the purpose of saving power and boosting energy efficiency, you ought to look for variable frequency drives (VFDs).
4. Plastic Washing System
Removes contaminants like dirt, labels, and adhesives, during others.
Importance of Key Factors:
- Choose from pre-washing and hot washing for superior washing of oily plastics.
- Deciding between a friction washer vs a float-sink tank depends on the type of contamination, especially heavy dirt and label removal.
- Reduces treatment costs and used water in a water recycling system.
- In order to remove moisture before extrusion, both centrifugal dryers and hot air drying are used for drying efficiency.
5. Sorting System
Plastic sorting technology separates various kinds of plastics or decreases impurities.
Importance of Key Factors:
- Optical sorters (NIR, laser) are more efficient for large-scale operations as compared to manual sorting methods.
- One useful method for separating PET from PP/PE is separation by density (float-sink).
- Metal detection and removal are essential for securing equipment that is downstream.
6. Plastic Pelletizing Machine
Turns into uniform pellets from cleaned and melted plastic.
Importance of Key Factors:
- By looking at Strand Pelletising to Underwater Pelletising, it matters to keep in mind that Strand Pelletising is simpler to solve, other than Underwater Pelletising is simpler and better at achieving high output.
- Multiple forms of cooling, such as using a water bath or air cooling, may affect the quality of the particles.
- Adjustable die size for different applications for a compatible pellet size.
- Dust collection ensures the manufacture of high-quality pellets that's clean.
Final Tips for Choosing a Washing Line:
- For material with high levels of contamination, extra washing stages may be needed to modify the system to suit your demands.
- Place a focus on water and energy efficiency to reduce long-term operating costs.
- Keeping a look at the future scalability of the line, is it ready for handling extra capacity in the case that it becomes needed?
- Look for reliable manufacturers that offer superior service as this refers to supplier reputation & after-sale support.
The most effective and cost-effective plastic recycling washing line can be selected by carefully evaluating each component in regard to your specific needs.
Conclusion
Plastic recycling washing lines are vital for recycling, and turn unhelpful waste into valuable assets. The crucial role of these systems will only grow as limits on the environment grow stricter and consumer demand for sustainable products increases.
Investing in the right machine for washing gives firms and recyclers a successful long-term position in the increasingly circular economy. High-grade plastic washing systems offer strong performance, superior material quality, and huge environmental benefits year after year with proper selection, applications, and maintenance.
Engaging with a skilled plastic recycling washing line manufacturer can assist organizations who are considering investing or raising plastic washing capabilities in determining the best solution for your specific needs and budget limitations. When set up correctly, the system could transform plastic waste from a challenge for the environment to an asset for its economy and the environment.
FAQs
1. Which kinds of plastic are suited for a washing line?
PET, PVC, HDPE, LDPE, and PP.
2. What is the water consumption of a washing machine for plastic?
Closed-loop applications of advanced systems recycle 80-90% of water.
3. Is it able to remove labels and glue from plastic?
Yes, adhesives will be removed effectively by chemical baths and friction washers.
4. How is a washing line different from a pelletizing line?
While pelletizing lines melt and turn plastic particles into pellets, washing lines clean them.
5. What is the duration of the washing procedure?
Duration varies between 30-60 minutes, depending on pollution levels.